- дача з будівельних блоків
- Склад формувальної суміші і порядок її приготування.
- Змішування компонентів суміші.
- Вплив вологості на дозрівання опілкобетона.
Застосування цементу зниженою марки - не рекомендується. При виготовлення опілкобетонних стінових каменів на віброобладнання обеспечівающімо гарне ущільнення жорсткої, опілкобетонних суміші, можливо знизити витрату цементу на 10-15%.
Склад бетону для шлакоблоків своїми руками
В якості наповнювача підійде шлак, зола, відходи горіння вугілля, відсів щебеню (каменю, граніту), відходи цегли, гравій, пісок, тирса (після обробки), керамзит, перліт, піщано-гравійна суміш, граншлак, залу, щебінь, тирса, гіпс, цегельний бій і т.д.
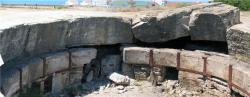
Процес виробництва саморобних бетонних блоків
Кладемо в форму з гіркою розчину, включаємо вібратор на 3-5 с, розчин осаджується. Якщо розчину мало - доповісти, потім вставити притиск і знову включити вібратор. Коли притиск «сяде» на обмежувачі - формування завершена. Залишилося включити вібратор на 5-10 с і зняти форму. Важливо! Форму потрібно знімати при працюючому вібраторі, тобто закінчення знімання повинно відбуватися вже на «вильоті». Сохнути блоки повинні 5-7 днів (а взагалі повне затвердіння шлакоблоків (або вібробетонних каменів) відбувається протягом місяця при температурі не менше 20 град і дотриманням умови високої вологості).
Продуктивність верстата при двох працівників 40-70 штук / год (від засипки до знімання форми 45 сек).
Додавання пластифікатора
Для пластичності блоків можна додати пластифікатор (5 грам на блок - міцність, водонепроникність і морозостійкість, менше тріщин) при вібролиття, можна і при вибропрессовании, але потрібно додавати занадто багато для ефекту, а це дорого.
Щоб шлакоблоки були міцними, потрібно враховувати:
Пісок потрібен великий;
Шлаки ідеальний доменний;
Цемент - якісний М400;
Устаткування - щоб краще пресованої, потрібно домогтися вибропрессования.
Час приготування і зберігання
Знімати з стрічки можна через добу. Повне висихання через пару місяців. Через день блоки вже можна носити - не ламаються, класти через тиждень.
При використанні пластифікатора готові блоки можна прибирати з майданчика і складувати вже через 6-8 годин. Без УПД - через дві доби. Зберігати готові шлакобетонові блоки потрібно в пірамідальних штабелях по 100 штук з невеликим (2-3 см) проміжком між блоками, щоб досихає «хатини».
На перших порах бетон можна готувати вручну. Згодом ефективніше і легше на електричній бетономішалці обсягом 0,2-0,5 куб.м.
Виробнича площадка - приміщення з рівною підлогою, добре провітрюваному місці / опаленням або рівний майданчик на вулиці під навісом.
Шлакоблоки - будівельні блоки, отримані вібропресуванням розчину бетону у спеціальній формі. Розмір стандартного блоку 390х190х188 мм з трьома отворами.
переваги шлакоблоків
низька собівартість;
висока швидкість будівлі з шлакоблоків;
хороша звукоізоляція;
хороша теплоізоляція;
можна виготовляти і для себе, і на продаж.
Негативні думки з виготовлення блоків з бетону своїми руками
Верстат вигідний лише при наявності дешевого або «халявного» сировини або ж при величезних обсягах робіт.
Пустотний блок, виготовлений де завгодно, дорожче, ділянки стіни такого ж розміру, зробленого методом знімною або незнімної опалубки, тим більше Ви витрачаєте свій час і сили. Тому, в основному, продаж цих верстатів - всього лише можливість заробити на інших.
Приклад витрат і вартості виготовлення саморобних блоків
На виробництво одного шлакоблоку йде 0,011 куб.м розчину, в пропорції 1: 7 (цемент: граншлак), тобто 1 мішок цементу = 36 блоків.
Законодавство
Постановами Уряду РФ від 13.08.97 № 1013, Держстандарту РФ № 86 від 08.10.2001 р та Держбуду РФ № 128 від 24.12.2001 р до переліку продукції, що вимагає обов'язкової сертифікації не належать будівельні бетонні блоки з різними наповнювачами (шлак, керамзит , опил і т. п.), а так само Вібропресс обладнання для їх виробництва.
Виготовлення форми своїми руками для лиття бетонних блоків
Форма для самостійного виготовлення шлакобетонних блоків являє собою ящик з 3-мм металу без дна з ручками. Щоб лицьова частина блоків була більш рівною, їх потрібно сушити на гумовій стрічці, змоченою розчином якого-небудь миючого засобу.
Стильна споруда з саморобних блоків
Все почалося з того, що одна сім'я вирішила реконструювати кухню будинку, збудованого 40 років тому. Коли рішення про розширення кухні було прийнято, за справу взялися архітектор та інженер.
пошуки матеріалу
На самому початку роботи власники будинку сказали, що їм байдуже, який реконструкції буде піддано будівлю, але в будь-якому випадку вони хочуть, щоб були збережені його первісний архітектурний стиль і матеріали, з яких будинок побудований. Встала цікава проблема, оскільки весь будинок був зведений з стінових блоків невеликого розміру, походження яких ніхто не знав.
Після бесід з багаточленними підрядниками, що спеціалізуються в області кладки, і місцевими постачальниками стало ясно, що забезпечити відповідність нового матеріалу того, з якого був побудований будинок, буде завданням не з легких. блоки представляли собою будівельний матеріал, за розмірами нагадував цеглу, але зроблений на основі піску і цементу і має характерну поверхню з "віспинами" крихітних пустот. У теперішній же час ці блоки в будівництві не застосовують.
Було вирішено, що коли почнемо розбирати стару кухню, збережемо якомога більше старих блоків. Але при спробі відокремити один блок від іншого нетривка зовнішня частина розламувалася, залишаючи неушкодженою тверду бетонну серцевину. Крім того, такі блоки можна було вважати прийнятним матеріалом, оскільки прибудова повинна була задовольняти більш строгим сучасним вимогам сейсмостійкості. Вирішили будувати каркас прибудови з дерева, а в якості зовнішньої обробки використовувати блоки. Таке рішення скорочувало потреби в блоках, але проблему все-таки не вирішувало.
Надалі дізнатися, що блоки, з яких побудований будинок, який свого часу привезли з м Фресно. Це була найбільша удача на той момент: дуже сподівалися знайти там завод, який і до цього дня виготовляє потрібні блоки. Виявилося, у Фресно налагоджено досить велике виробництво піску, гравію і цементу і що безліч невеликих компаній випускають на цій основі різноманітні будматеріали. Однак жодна з цих компаній не виготовляє блоки на зразок тих, що ми хотіли б придбати. Було потрібно у всьому розібратися на місці.
мальовничі руїни
Більшість складів будматеріалів у Фресно були закриті з нагоди вихідних, а на єдиному складі, який в цей день працював, нічого не змогли запропонувати. Експедиція, судячи з усього, повинна була закінчитися невдачею. На зворотному шляху додому в невеликому містечку, під'їжджаючи до газозаправної станції, ми побачили мотель, збудований з матеріалу, який розшукували. Ретельний огляд будівлі підтвердив перше враження - матеріал, з якого воно було побудовано, виявився абсолютно ідентичним нашим блокам, аж до оздоблювальних елементів, використаних в віконних отворах. Озирнувшись довкола, помітили ще чотири будівлі, збудовані з таких же блоків.
Розпитавши декількох чоловік, ми з'ясували, що коли-то в цих місцях існувало невелике підприємство по виробництву блоків, але воно дотла згоріло, і ніхто точно не знав, де воно тоді розташовувалося. Нам порадили проїхати по дорозі в кар'єр, який тут до сих пір функціонував, і пошукати там сторожа. Ми спустилися в кар'єр і зрозуміли, що сьогоднішній день був прожитий не дарма - зустрівся по дорозі великий ангар, маленький магазин, флігель і два напівзруйнованих будинки були складені колись з «наших» блоків. Крім того, обійшовши навколо магазин, були виявлені акуратно складені в штабель блоки для зовнішніх підвіконь точно такого типу, які нам були потрібні. Їх налічувалося штук 50, і вони були чудовою форми і відповідного кольору, який, можливо, лише злегка вицвів. Тут мабуть колись стояв завод: плити фундаменту згорілого будинку були як і раніше на місці, як і якесь іржаве обладнання, ідентифікувати яке було неможливо. Однак, крім підвіконних блоків, тут не знайшлося нічого такого, що можна було використовувати. але біля руїн стояв причіп , В якому жив сторож.
сюжет заплутується
Сторож розповів, що матеріал, який тут добували, називається пемзою. За його уявленням її червонуватий колір виходить завдяки залозу, що міститься у верхніх шарах кар'єра. Глибше в кар'єрі колір матеріалу блякне і переходить від червоного відтінку до рудувато-коричневого, а потім до сірого і білого. Білий матеріал в найбільш глибокій частині кар'єра нагадує Талькова пудру і називається пуццоланом. Будівельні компанії використовують його в якості добавок при виробництві бетону. Це все, що наш співрозмовник зміг нам повідомити. По поверненню додому, ми вже знали, яким повинен стати наш наступний крок. Вирішено виготовити блоки своїми силами.
видобуток сировини
На наступний день разом з архітектором вирушили у Фресно на великому самоскиді, прихопивши штати і кирки. Площа кар'єра становила більше двох квадратних кілометрів, а глибина - близько 30 м. І поки ми обходили навколо кар'єра в пошуках потрібного нам матеріалу, все вкрилися пилом і потом. Борти кар'єру були тверді як камінь, але при розтиранні матеріал перетворювався в пилоподібний порошок. Після ретельного пошуку знайшли місце, де колір пемзи був майже таким, який нам був потрібний. Саме тут і вирішили приступити до справи. Але поглянувши на наші кирки і лопати, господар кар'єра засміявся. "Вам доведеться дуже довго потіти, якщо ви збираєтеся копати вручну, - заявив він. - Я знаю більш ефективний спосіб". З цими словами він нас покинув і через кілька хвилин повернувся на невеликому екскаваторі.
Після того як завантаження була завершена, ми накинули на наш дорогоцінний матеріал брезент, а поверх брезенту поклали сорок найкращих підвіконних блоків, обраних з штабеля, який напередодні виявили.
Виготовлення блоків і кладка
Тепер у нас було сировину для виробництва блоків. Але ось технологію цього виробництва ми не знали. І взялися експериментувати. Суміш, рецепт якої досвідченим шляхом був, врешті-решт, знайдений, складалася з води, піску, цементу, барвника і подрібненого мінералу, здобутого нами в кар'єрі. Для приготування бетону використовували ручну бетономішалку і крутили її для приготування одного замісу мінімум десять хвилин. Незважаючи на те, що мінерал був дуже близький за кольором старим блокам нашого будинку, колір суміші змінювався в міру додавання в неї інших складових, необхідних для надання міцності і потрібної текстури. Зрештою, ми вирішили і цю проблему методом проб і помилок. Виготовили велику серію зразків, вказавши на кожному точний тип і кількість використаного барвника і інших складових, перш ніж знайшли підходяще співвідношення частин суміші. Нові блоки після виготовлення сушили, до набуття ними остаточного кольору, цілий тиждень.
Перші зроблені форми, які були виготовлені з тонколистового металу, ми відкинули. Справа в тому, що навіть при використанні більшої кількості дизельного палива в якості мастила бетон прилипав до цих форм, і поверхні блоків виходили шорсткими і не влаштовували нас. Рішення, яке було знайдено, позначилося досить простим. Було виготовлено дерев'яні рами, розділені таким чином, щоб в них можна було відливати одночасно п'ять блоків (це гранична кількість, з яким одна людина могла легко впоратися). Для закруглених кутів, які були потрібні на елементах обробки, ми додали до форм вставки з тонколистового металу. Коли приступили до відливання блоків, то намагалися точно дотримуватися співвідношення частин суміші, щоб звести до мінімуму відмінності (в першу чергу за кольором) між блоками в різних партіях. Що ж стосується забезпечення відповідності текстурі первинних блоків, то необхідні нерівності отримали, відмовившись від надто ретельної трамбування бетонної суміші при заповненні форм і чищення їх під час вивантаження готових блоків.
Форми з бетонною сумішшю на перші 24 години закутали плівкою, щоб зберегти поверхню більш вологою дня рівномірного схоплювання бетону. На другу добу блоки вийняли з рами і акуратно поклали в штабель, а через тиждень їх вже важко було розбити молотком. Для реконструкції кухні потрібно 600 блоків. Однак для впевненості вирішили виготовити кілька більше, ніж було потрібно. За день ми робили приблизно 75 блоків, і вже скоро задній двір був заповнений штабелями новеньких виробів, що дозрівають під нежарким сонцем пізньої осені. Витративши багато часу і зусиль на виготовлення блоків, ми захотіли знайти каменяра, який би звертався з цими витворами наших рук як зі злитками золота, упакованими в пластикову вибухівку. Як виявилося, власники будинку знали муляра з хорошою репутацією. І вже незабаром ми змогли спостерігати, як він їх укладав. Відповідність старої кладки було повним. Зараз ні за матеріалом, ні за колірною гамою зовнішні стіни кухні-прибудови нічим не відрізняються від інших частин будинку. І ніщо не говорить про те, скільки праці все це вимагало. Чи були ці зусилля виправдані? Хто знає. Однак власники будинку отримали те, чого вони бажали, ми ж задовольнилися тим, що зуміли вирішити проблему, яка здавалася нерозв'язною.
Незнімна опалубка з пінополістиролу для будівництва лазні або будинку
Світ навколо безперервно розвивається, відкриваються нові горизонти в автомобілебудуванні, з'являються новітні розробки у всіх сферах життя, стрімко ростуть міста. Разом з цим удосконалюються і технології будівництва. Найбільш сучасної та популярної технологією, яка використовується для зведення будівель, є метод із застосуванням незнімної опалубки. Він використовується для побудови практично будь-яких будівель, починаючи від спортивних комплексів і житлових багатоповерхових будинків і закінчуючи басейнами, котеджами і адміністративними корпусами. Незнімна опалубка являє собою термоблоки з пінополістиролу довжиною в 1 метр, а шириною і висотою в 25 см. Використання незнімна опалубка має величезні переваги перед іншими способами будівництва. Ця технологія високоекономічними як у фінансовому плані, так і в швидкості будівництва.
Зведення будівель відбувається до 10 разів швидше, а простота установки незнімної опалубки дозволяє використовувати низькокваліфікованих працівників. Термін служби нових будівель з використанням даної технології перевищує 100 років. За допомогою незнімної опалубки можна не тільки зводити нові будівлі, а й проводити капітальний ремонт старих будівель. Хоча незнімна опалубка досить давно визнана фахівцями в галузі будівництва і використовується більш ніж в 40 країнах світу, більшість вітчизняних виробників адаптували цю технологію для кліматичних умов Російської федерації та країн СНД.
Стіни, зведені з використанням незнімної опалубки, не тільки прекрасно захищені тепло- і звукоізоляцією, а й не пропускають вологу, не дивлячись на те, що їх товщина майже вдвічі менше цегляних. Що важливо, бетонування опалубки можливо і при мінусовій температурі без втрати якості заливки. Це властивість широко використовується при будівництві бань, саун, індивідуальних басейнів. Завдяки високій точності виготовлення при складанні опалубки не потрібно закріплюють розчинів. При будівництві стін з цегли неминучі порожнечі в поверхні, що ускладнює подальшу заливку бетоном. Стіни ж з опалубки не мають таких отворів.
Ще однією перевагою цієї технології є те, що існує можливість економії і на інших частинах будівлі. Наприклад, через легкості конструкції, побудованої за допомогою незнімної опалубки, можна заощадити до 30% коштів, призначених для зведення фундаменту, також можна використовувати нові типи економічного фундаменту. Технологія незнімної опалубки не вимагає присутності на будівельному майданчику важкої техніки. Цей спосіб може застосовуватися в сейсмоактивних зонах і зонах з проблемним грунтом. Крім того, виробництво опалубки не завдає шкоди екології і є повністю безвідходним. Цікаво відзначити, що стіни з незнімної опалубки можуть бути закругленими практично з будь-яким радіусом, відкриваючи нові можливості для проектування і дизайну майбутніх будівель, при цьому, не втрачаючи перерахованих вище характеристик. Можливо, в найближчому майбутньому з'являться більш унікальні будівельні технології, але на сьогодні методика із застосуванням незнімної опалубки є найбільш передовою і досконалою.
БЛОКИ СВОЇМИ РУКАМИ
Стінові блоки давно стали одним з найпоширеніших будівельних матеріалів. Їх випускають розмірами 390x190x19С мм, рідше 510х380х198 мм. Я ж розповім про самостійне виготовлення блоків.
Блоки своїми руками Розміри блоків я Вибравши 510x250x215 мм (ОБСЯГИ в 14 цегли). З відходів листового заліза Звара 11 форм без днищ. З боків приваривши по 2 ручки. Прямо на землі розстеляли руберойд, ставлю форму. Щоб суміш НЕ схоплює зі стінкамі форми, зсередини протираю їх ганчіркою, змоченою відпрацьованім маслом або солярки. Засінаю туди жорсткий керамзитобетон. Трамбують НЕ Надто сильно. Першу форму знімаю після засипки 11-ої - це приблизно через 10-12мін. Блоки стояти на місці в течение 12 рік. Потім перекладав їх під навіс. Тверднуть смороду при плюсовій температурі в течение 24 діб. Навіс роблю з руберойду, брезенту або поліетиленової плівки. Під ним блоки будут захіщені від дощу и сонця.
Блоки своїми руками Пробував виготовляти блоки і з порожнечами. Вставляти два дерев'яних кругляків, обточених на конус и обгорнутіх покрівельнім залізом. Пустотоутворювач можуть бути круглі, квадратні, прямокутні ... Залежно від того, як укладені блоки, товщина стін виходить 215, 250 або 510 мм.
Для Товсте стін блоки краще делать порожністімі, для тонких - заповнений. Умовно стіни товщиною 215мм без пустот можна назвати холодними, 250мм - напівтеплі, 510мм з пустотами - теплими.
Для виготовлення половині блоків в форму по центру вставляю лист заліза. В заготовки, Які Використовують для формирование отворів у стіні будинку, доводиться згадуваті дерев'яні пробки для закріплення дверних и віконніх коробок.
Блоки своїми руками Пробував робити блоки, застосовуючи вібратор, але розчин йде на дно форми і керамзит не зв'язується. Щоб цього НЕ відбувалося, Звара Загальну форму для декількох блоків. Вібратор закріплював збоку. Стінкі форми робів вищє на 1/3 - це для усадки бетону во время вібрації.
Заповнювачами можуть бути місцеві недефіцитних матеріали: керамзит, шлак, тирса і т.д. Я для Приготування суміші вікорістовував цемент, керамзит и пісок в співвідношенні 1: 4: 1.
Найважча робота - Приготування бетону. Щоб трохи полегшити її, спочатку виготовив ручну бетономішалку з двохсотлітрову бочки. Вісь обертання її зміщена на 10 см щодо центру. Усередині приварив хрестовини. Таким чином, за рахунок ексцентрикового обертання бочки і завдяки хрестовини забезпечувалося гарне перемішування маси. За 8 оборотів бочки розчин був готовий.
Таким чином виготовив 500 блоків. Їх вистачило для кладки теплого хліва розміром 6,2x4 м і прибудови до нього - холодного сараю.
Незважаючи на те, що блоки значно більше за розміром і масою, ніж звичайний червона цегла, прийоми кладки і комплект інструмента залишаються тими ж. Також дотримуються перев'язка кладки в кутах і на прямих ділянках стін. На початку кладки з блоків бажано на цоколі або фундаменті (після гідроізоляції) зробити пояс з червоної цегли. Він повинен виступати назовні від цоколя на 30-40 мм, захищаючи останній від намокання.
дача з будівельних блоків
Опис video матеріалу:
будівництво дачі з блоків
Склад формувальної суміші і порядок її приготування.
Цемент.
Для приготування формувальної суміші рекомендується застосування портландцементу марки не нижче М-400.
Застосування цементу зниженою марки - не рекомендується.
При виготовлення опілкобетонних стінових каменів на віброобладнання обеспечівающімо гарне ущільнення жорсткої, опілкобетонних суміші, можливо знизити витрату цементу на 10-15%.
Зниження витрати цементу обумовлено тим, що ущільнені жорсткі бетони мають велику міцність в порівнянні з рухомими бетонами, при однаковій витраті цементу.
Середня насипна щільність цементу 1200кг / м3.
Пісок.
Технологія виготовлення опілкобетонних блоків методом об'ємного вібропресування з негайною розпалубкою, передбачає застосування жорстких, формувальних сумішей.
Для приготування такої суміші необхідний пісок певних характеристик.
В якості основного заповнювача, рекомендується застосовувати пісок великої або середньої фракції, здатний створити
міцний скелет сприймає навантаження, при формуванні та транспортування блоків на ділянку сушки.
В основну масу піску великої фракції (3.5 - 2.4 МК) рекомендується додавати пісок середньої або дрібної фракції (2.5-1.5 МК).
Суміш піску великих і дрібних фракцій ідеальний матеріал для приготування жорстких формувальних сумішей.
Однак в піщаної суміші частка дрібного піску не повинна перевищувати 10%. В іншому випадку різко знижується міцність бетону на такому піску, збільшується відсоток браку при вибропрессовании стінових каменів.
Збільшення смачиваемой поверхні, при використанні дрібного піску, призводить до перевитрати води і вимагає підвищеної уваги при виробництві формувальної суміші.
Також необхідно уникати застосування піску з підвищеним вмістом глинистих і пилуватих включень.
Вміст глини не повинно перевищувати 0.5%, кількість пилуватих включень не більше 3% від загальної маси.
Застосування в опілкобетонних піску підвищеної крупності (3.0-3.5) і щебеню не допускається.
У разі, якщо застосування природного піску необхідної фракції неможливо, рекомендується застосування штучних пісків, відходів пиляння вапняку, шлаку паливного і доменного, золи винесення ТЕЦ і т. Д.
Основні вимоги викладені вище зберігаються і для цього матеріалу.
В основному при виборі піску слід керуватися вимогами ГОСТів (ГОСТ 8736-93).
Сухий річковий пісок середньої групи (2.5-1.9 Мк) має насипну щільність 1500 кг / м3. Якщо вологість піску 5%, насипна щільність зменшується до 1300 кг / м3.
Опілкобетонниє стінові блоки, на 40-50% складаються з деревної тирси, частка підготовленої, піщаної суміші відносно невелика, тому варто підійти до питання вибору інертних матеріалів з максимальною відповідальністю.
Правильно підібраний інертний заповнювач дозволяє значно знизити витрату дорогого цементу.
Група піску Модуль крупності Мк.
Дуже невеликий 3.0-3.5
великий 2.5-3.0
середній 2.0-2.5
Дрібний 1.5-2.0
Дуже невеликий менш 1.5
Вода.
Для приготування жорсткої опілкобетонних суміші не рекомендується застосовувати воду забруднену жирами, солями, цукрами та іншими включеннями.
Допускається застосування морської води при помірному змісті солей.
В цілому бажано застосовувати воду відповідає вимогам ГОСТа- 23732-79.
Деревна тирса.
Для виготовлення опілкобетонних стінових каменів можливе використання тирси практично всіх порід дерев, проте тирсу з дерев хвойних порід менше схильні до гниття.
Тирса можуть бути використані, як після спеціальної підготовки, так і без підготовки.
Підготовка тирси включає в себе витримку під навісом протягом 2-3 місяців.
Саме в цей час, свіжі тирсу інтенсивно виділяють органічні речовини, що уповільнюють тверднення цементу.
Даний спосіб стримує можливості виробництва стінових каменів.
Необхідність організувати криті склади сировини (тирси) може призводити до значного розширення необхідних виробничих площ і збільшення накладних витрат.
Позитивна сторона цього методу - найменший витрата захисно-модифікуючий складу, необхідного для виробництва якісного опілкобетона.
Тирса не пройшли витримку, відразу подаються на ділянку змішування, обробка тирси захисними складами відбувається безпосередньо в змішувачі.
Даний метод забезпечує максимальну продуктивність, при виготовленні опілкобетонних стінових каменів.
Однак при такому методі дещо зростає витрата захисно-модифікуючий складу.
Більшість діючих підприємств виробляють опілкобетонниє стінові блоки працюють саме на непідготовленого тирсі.
Також можливий ще один спосіб підготовки тирси.
Тирса подається в змішувач, де перемішуються з захисними складами, розчиненими в невеликій кількості води.
Потім оброблені тирса вивантажуються із змішувача і витримуються під навісом 2-3 дні.
Після закінчення цього часу оброблені тирса можуть бути використані для приготування опілкобетонних, формувальної суміші.
Даний спосіб забезпечує максимальну якість підготовки тирси перед їх безпосереднім використанням.
Середня насипна щільність деревної тирси хвойних порід 220-250 кг / м3.
Основні добавки.
Для нейтралізації виділяються тирсою органічних речовин, а також для зниження часу твердіння опілкобетона, необхідно застосовувати добавки.
При виробництві стружкобетону рекомендується застосування хлориду кальцію, сульфату амонію, вапна, або рідкого натрієвого скла.
З перерахованих речовин, найбільш ефективним і зручним в роботі, є хлорид кальцію.
При невисокій вартості, хлорид кальцію забезпечує надійний захист тирси в бетонній масі.
Застосування хлориду кальцію дозволяє значно зменшити час витримки відформованих блоків. Вже через 5-8 годин (температура в цеху 15-25 З) блоки можуть укладатися в штабелі до п'яти рядів.
Хлорид кальцію може подаватися в змішувач, як в сухому вигляді, так і розчинений у воді.
Також при виготовленні опілкобетонних стінових блоків (каменів) можливе застосування гидрофобизирующих добавок бетону, захисних просочень деревини, вогнезахисних складів.
Рухливість (жорсткість) бетону.
Для отримання якісних опілкобетонних стінових блоків (каменів), необхідно приготування малорухомої (жорсткої) формувальної суміші.
Саме жорстка пескоцементного суміш використовується при виготовленні стінових блоків методом об'ємного вібропресування
Жорсткість суміші - основний параметр, що забезпечує якість формованих виробів, при їх негайної розпалубки.
Метод напівсухого вібропресування забезпечує високі показники міцності, морозостійкості та довговічності стінових каменів при помірній витраті цементу.
Зауважимо, що абсолютна більшість опілкобетонних стінових блоків (каменів) використаних при будівництві 50-60 років (розквіт застосування органічних наповнювачів в нашій країні) отримували методом лиття в розбірні форми з незначним ущільненням матеріалу в формі.
При відсутності якісного цементу і добавок, що модифікують отримання якісного, довговічного будівельного матеріалу з використанням органічних наповнювачів практично неможливо!
Метод об'ємного вібропресування на якісному обладнанні забезпечує значне ущільнення матеріалу, практично не використовувався в цивільному будівництві 50-60 років.
Водоцементне співвідношення (ВЦ).
Рухливість (жорсткість) суміші залежить від водоцементного співвідношення (ВЦ).
Для методу напівсухого вібропресування характерно водо-цементне відношення 0.4.
Зауважимо, що таке співвідношення близько до ідеального для протікання процесу гідратації цементу.
При проведенні випробувань марки цементу по міцності на вигин і стиск рекомендовано саме водо-цементне відношення 0.4, так як прітаком співвідношенні контрольні зразки показують максимальну міцність на стиск і розтяг.
Суміші умовно діляться на жорсткі, малорухливі, рухливі і литі
Для визначення рухливості суміші в індустріальному будівництві використовується еталонний конус.
При виробництві опілкобетонних стінових блоків (каменів) в умовах малих і середніх підприємств, рухливість отриманої суміші можна визначити в такий спосіб.
При стисненні в кулаці суміш не повинна розсипатися, на грудці повинні явно віддрукуватися пальці, а на долоні не повинно залишатися зайвої вологи.
Хорошим показником правильно підібраною жорсткості суміші є поява на відформованої блоці цементного молочка.
У місці зіткнення відформованої блоку з піддоном не повинно спостерігатися водяного буртика, що свідчить про надлишок вологи в розчині.
Перезволожений суміш значно гірше піддається віброущільнення, ніж суха, підвищений вміст води викликає труднощі при розпалублення виробів.
Відформовані стінові блоки при зайвому вмісті води «пливуть» на формувальному піддоні і можуть руйнуватися в процесі транспортування на ділянку сушки.
При нестачі води, спостерігається поява тріщин на поверхні расформованного блоку.
Нестача води в формувальних сумішах збільшує відсоток виробничого браку і знижує міцність виробу.
Правильний підбір змісту води в формувальної суміші - першочергове завдання при отладке5 технології виготовлення стінових блоків (каменів).
Необхідно стежити за стабільної повторюваністю одержуваних сумішей і безпосередньо самих стінових каменів.
Базовий склад опілкобетонних суміші марки М-50. D-1100 кг / м3.
Цемент M 400 200 кг / 166л
Пісок Мк 2.0 2.5
590 кг / 393л
Тирса хвойних порід 200 кг / 800л
Хлористий кальцій та інші добавки 5 кг / 4.5л
Вода біля 100літров (в залежності від вологості використовуваних матеріалів).
Змішування компонентів суміші.
Існує кілька способів приготування жорстких формувальних опілкобетонних сумішей.
Для приготування формувальної суміші необхідний змішувач примусової дії.
Застосування гравітаційних змішувачів не може бути рекомендовано, через незадовільну якість перемішування жорстких сумішей.
Розглянемо два основних способи отримання опілкобетона суміші придатною для виготовлення блоків
У змішувач подаються
тирса,
цемент,
пісок,
ретельно перемішуються,
потім малими порціями,
через живлять форсунки подається необхідна кількість води.
Таким способом можна отримувати жорстку формувальну суміш щільністю 900-1800 кг / м3 (в сухому стані) придатну для віброформованія опілкобетонних блоків.
Для отримання більш легкої опілкобетонних суміші (зміст тирси більше 40%) рекомендований інший порядок змішування і подачі матеріалів.
В працюючий змішувач подаються
тирса,
потім через живлять форсунки подається вода,
близько 25% від повного обсягу.
Тирса перемішуються,
рівномірно змочуючи.
Потім невеликими порціями подається цемент.
Швидкість подачі цементу необхідно відрегулювати в залежності від типу змішувача, форми робочих лопатей, швидкості обертання активатора, а також загальної ефективності перемішування легкої суміші даними змішувачем.
Цемент, що подається невеликими порціями, рівномірно огортає змочені тирсу.
При правильно підібраною швидкості подачі цементу, форми робочих лопатей, швидкості обертання ротора змішувача відбувається рівномірне нанесення цементу без утворення грудок і не промісити ділянок.
Потім подається основна маса цементу і піску, після нетривалого змішування подається вода.
Таким способом можна отримувати опілкобетонних формувальну суміш щільністю 800-600 кг / м3 (в сухому стані).
Добавки, захисні склади і прискорювачі твердіння бетону розлучаються у воді або подаються в сухому стані.
Вплив вологості на дозрівання опілкобетона.
Міцність відформованих стінових каменів залежить не тільки від кількості і якості цементу, а й від умов дозрівання стінових каменів.
Технологія виготовлення опілкобетонних стінових каменів (блоків) передбачає можливість отримувати якісний будівельний матеріал без застосування пропарювальних і сушильних камер.
Відмова від застосування енергоємних пропарювальних (сушильних) камер дозволяє скоротити початкові витрати на організацію виробництва, а також істотно знизити собівартість виробів, що випускаються.
Однак для оптимізації режиму дозрівання стінових блоків (каменів) рекомендується проведення наступних заходів.
Відформовані стінові камені (блоки) на піддонах подаються на ділянку попередньої сушки.
Через 5-12 годин (в залежності від температури на ділянці сушіння) вироби і штабелюються на транспортних піддонах.
Зауважимо, що вироби, відформовані 5-12 годин тому, набрали не більше 10-15% розрахункової міцності, подальший набір міцності повинен відбуватися в певних умовах.
Відомо, що при дозріванні блоків в природних умовах на відкритому повітрі, без додаткового зволоження міцність виробів знизиться вдвічі від можливої!
Тому стінові блоки укладені на транспортні піддони ретельно ховаються целофановою плівкою, для запобігання втрати вологи.
Блоки витримують в закритому вигляді 5-7 днів.
Проведені заходи дозволяють отримувати якісний стіновий матеріал без пропарювання і просушування.
Економіка виробництва опілкобетонних блоків.
Для виготовлення повнотілої стінового опілкобетонного каменю (390х190х190) марки М-50 буде потрібно:
Цемент М-400 3,2 кг / 2,6 л
Пісок 9,4 кг / 6,2 л
Хлористий кальцій 0,16 кг / 0,145
Тирса деревинна 3,2 кг / 12,8 л
Всього: 15,96 кг / 21,7л
Вартість матеріалів (для Житомирської обл. На 01.02.09)
Цемент М-400 1 грн. кг (вартість фасованого цементу, при купівлі цементу «навалом» вартість може бути нижче)
Пісок річковий з привозимо 5 копійок за кілограм. З розрахунку вартості 10000 кг (а / м КАМАЗ) - 500 грн.
Хлористий кальцій 5 грн. за кілограм.
Тирса 30 грн. за тонну (з урахуванням доставки до місця виробництва. Якщо ж Ви, переробляє свої відходи виробництва - безкоштовно).
Цемент М-400 3.2 кг х 1 грн. = 3 грн. 20 коп.
Пісок 9.4 кг / 6.2 л х 5 коп. = 47 коп.
Хлористий кальцій 0.08 кг / 0.072 л х 5 грн. = 40 коп.
Тирса деревинна 3.2 кг /12.8 л х 3 коп. = 10коп.
Всього: 4 грн. 17 коп
Для виготовлення пустотного (33% пустотности) опілкобетонного каменю марки М-35 витрата матеріалів знижується на 33%.
Вартість матеріалів складе 4 грн. 17 коп. - 33% = 2 грн. 70 коп. Або одного куба 62 х 2 грн. 70 коп. = 171 грн. 74 коп